Selecting the appropriate grating material is crucial for various industries. Understanding the distinctions between FRP fiberglass grating and steel grating is essential. The comparison aims to shed light on their unique characteristics, benefits, and applications. As the demand for FRP grating continues to rise in sectors like petrochemicals, water treatment, and oil & gas, it’s evident that this lightweight and corrosion-resistant alternative offers unmatched advantages over traditional steel options. OceanFRP specializes in manufacturing top-quality FRP Molded Grating and FRP Pultrusion Grating, providing solutions that include phenolic FRP grating, micro mesh grating, and mini mesh grating to meet diverse industrial needs.
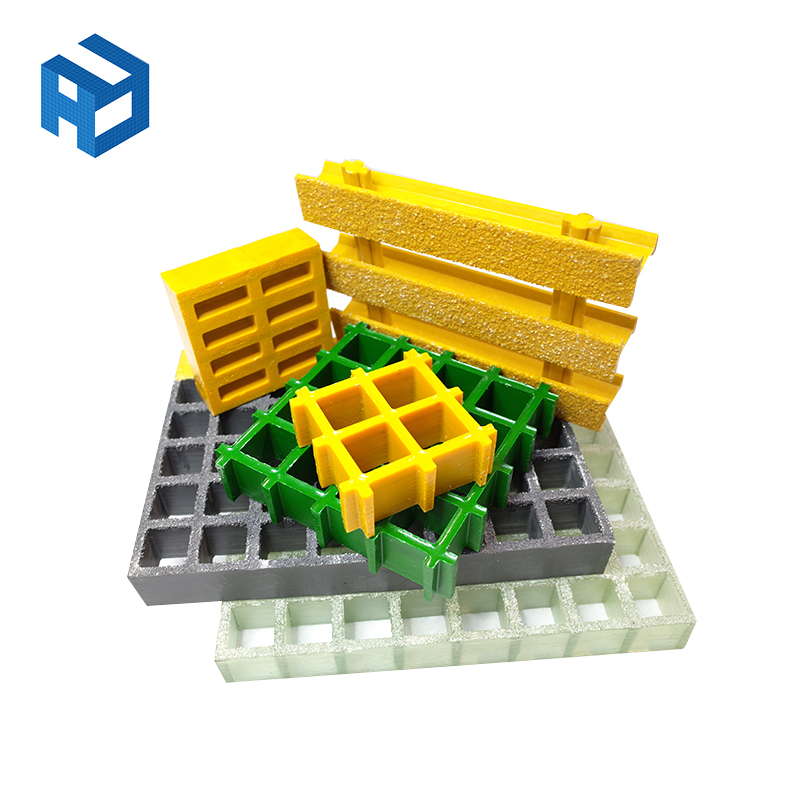
Introduction
Brief Overview of Grating Materials
FRP grating, a composite material made from fiberglass reinforcements and a resin matrix, offers a combination of strength, corrosion resistance, and durability. It is widely used in walkways, stair treads, platforms, and various other applications. The properties of FRP grating include corrosion resistance, high strength-to-weight ratio, UV resistance, minimal thermal expansion, low electrical & thermal conductivity, and an anti-skid surface. This versatile material is ideal for applications ranging from chemical plants requiring corrosion resistance to power plants needing excellent electrical insulation. Its structural integrity allows it to be weight-bearing between spans. The advantages of FRP grating over steel are significant – its strength, lightweight nature, corrosion resistance, non-conductivity, safety features, and long-term cost-effectiveness make it a superior choice for industrial needs.
Importance of Choosing the Right Grating Material
Selecting the appropriate grating material is crucial for industries looking for durable and cost-effective solutions. FRP grating does not corrode like steel grating and is therefore preferred in corrosive environments to reduce maintenance costs. Its versatility extends to various applications such as walkways and overhead platforms. With exceptional properties like corrosion resistance and a high strength-to-weight ratio, FRP grating stands out as a top choice for demanding environments. When considering factors like longevity, safety features, and overall performance in different conditions, choosing FRP grating proves to be a wise investment that ensures reliability and durability in the long run.
What is FRP Fiberglass Grating?
FRP Fiberglass Grating, also known as Fiber Reinforced Plastic Grating, is a composite material that combines fiberglass strands with a resin matrix. This innovative construction results in a durable and versatile product that offers exceptional strength and corrosion resistance. The composition of FRP grating ensures it is impervious to corrosive elements like chemicals, saltwater, and extreme weather conditions, making it ideal for various applications.
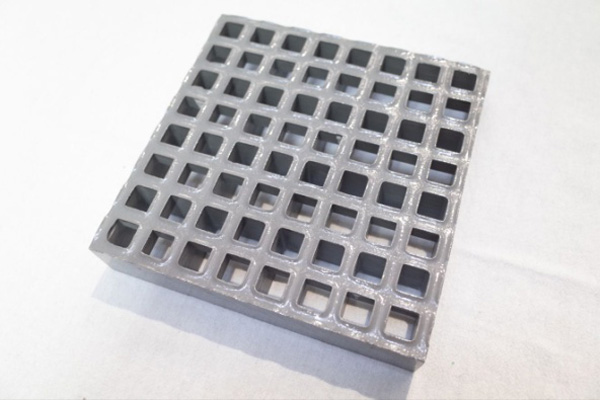
Common applications
- Chemical Plants: Due to its corrosion-resistant properties, FRP grating is extensively used in chemical plants where exposure to harsh chemicals is common.
- Oil & Gas Industries: The durability and lightweight nature of FRP grating make it suitable for offshore platforms and refineries.
- Water Treatment Facilities: Its resistance to water-related corrosion makes FRP grating ideal for use in water treatment facilities.
- Industrial Walkways: The anti-slip surface of FRP grating ensures safety in industrial walkways where traction is essential.
- Commercial Buildings: From office buildings to shopping centers, the versatility of FRP grating allows for diverse applications.
By choosing FRP fiberglass grating, industries benefit from its high load capacity, impact resistance, and long-term cost-effectiveness compared to traditional steel options.
What is Steel Grating?
Definition and composition
Steel grating, a versatile structural material widely employed for its high strength, load-bearing capacity, and durability, consists of steel bars or wires welded or locked together at right angles. This construction ensures a rigid and durable product that can withstand heavy loads and harsh conditions in industrial settings. The various types of steel grating, such as welded steel grating, press-locked grating, and swage-locked steel grating, offer unique features and benefits tailored to specific project requirements.
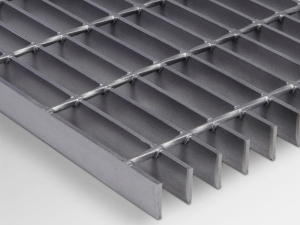
Common applications
- Bridge Flooring: Steel grating is commonly used in bridge flooring due to its strength, durability, and resistance to pests and rot.
- Trench Covers: Its high load capacity makes steel grating ideal for covering trenches while ensuring safety and stability.
- Walkways: Steel grating provides slip resistance on walkways in industrial environments where traction is essential for worker safety.
- Ramps: The durability of steel grating makes it suitable for use on ramps where it can withstand heavy foot traffic.
- Platforms: In industrial facilities, platforms made from steel grating offer stability and longevity for various operational needs.
Steel grating’s ability to resist corrosion combined with its strength and durability makes it a popular choice for diverse applications requiring robust structural support.
Key Differences Between FRP Fiberglass Grating and Steel Grating
- Strength and Durability
FRP grating, known for its exceptional strength and durability, outperforms steel grating in various aspects. The tensile strength of FRP grating is unmatched, offering a reliable solution for heavy-duty applications. In terms of resistance to environmental factors, FRP grating excels by being impervious to corrosive elements like chemicals and saltwater. This makes it an ideal choice for industries requiring long-lasting and robust materials. Moreover, the longevity of FRP grating in various conditions ensures a sustainable investment that withstands the test of time.
-
Weight and Handling
When comparing the material weights of FRP fiberglass grating and steel grating, it’s evident that FRP is significantly lighter, weighing 30% less than aluminum grating and 75% less than steel grating. This lightweight nature simplifies installation and transportation, reducing labor costs and saving time during the setup process. The impact on labor and cost is minimized with FRP grating due to its ease of handling, making it a cost-effective solution for industries looking to streamline their operations.
-
Corrosion Resistance
In terms of performance in corrosive environments, FRP fiberglass grating stands out by being corrosion-resistant to chemicals, saltwater, and extreme weather conditions. Its minimal maintenance requirements make it a hassle-free option for industries where upkeep costs are a concern. The ideal usage scenarios for FRP grating include applications that demand durability, longevity, and resistance to harsh elements like corrosive substances or outdoor exposure.
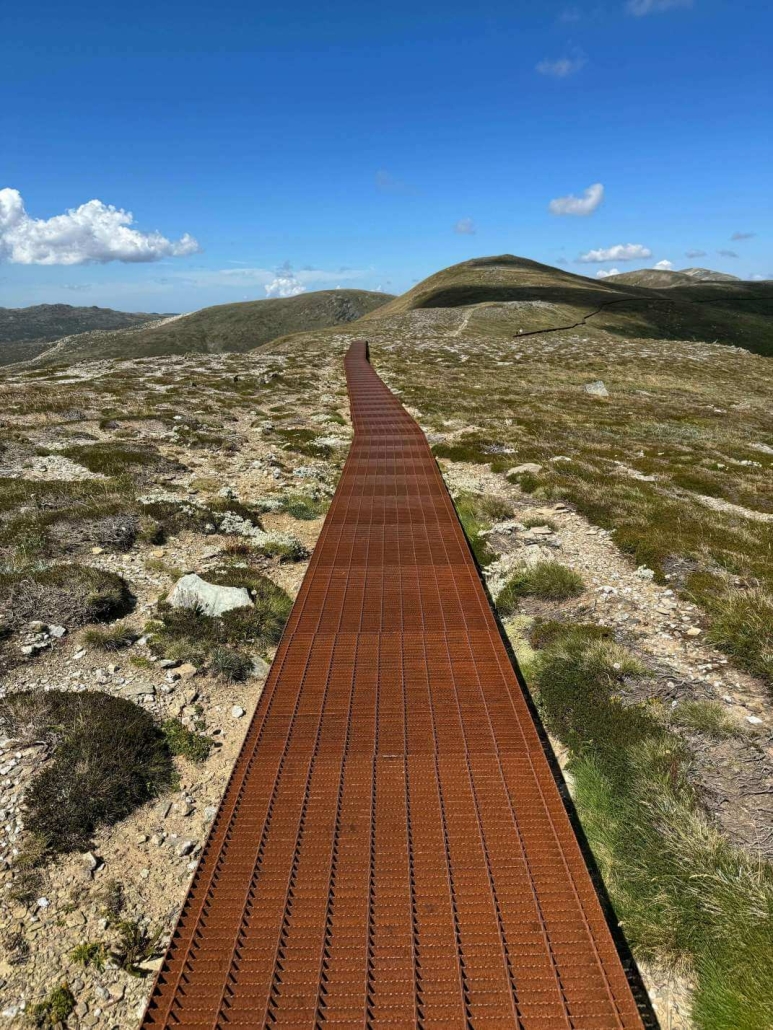
-
Safety
When it comes to safety considerations, FRP grating offers distinct advantages that prioritize the well-being of individuals in various environments. The slip resistance of FRP grating ensures secure footing, reducing the risk of accidents in areas prone to moisture or spills. Additionally, its fire resistance properties provide an added layer of safety, crucial for applications where fire hazards are a concern. The overall impact on workplace safety is significant with FRP grating due to its durable and non-conductive nature, minimizing risks associated with electrical conductivity and structural failures.
-
Cost Analysis
Analyzing the costs associated with grating materials reveals compelling reasons to consider FRP fiberglass grating over traditional steel options. The initial cost comparison showcases that while steel grating may have a lower upfront expense, the long-term benefits of FRP grating outweigh this initial investment. With minimal maintenance requirements and exceptional durability, FRP grating proves to be a cost-effective solution over time. The long-term cost implications further highlight how choosing FRP can lead to substantial savings in maintenance and replacement costs compared to steel alternatives. Ultimately, the return on investment for industries opting for FRP grating is evident through reduced operational expenses and enhanced longevity.
-
Aesthetic and Customization Options
The aesthetic appeal and customization capabilities of FRP fiberglass grating offer versatility and design flexibility for various applications. The availability of colors and finishes allows industries to match their grating solutions with existing aesthetics or branding requirements seamlessly. Moreover, the extensive customization capabilities enable tailored solutions that meet specific project needs, ensuring both functionality and visual appeal are achieved simultaneously. Whether it’s creating unique patterns or incorporating company logos into the design, FRP grating provides endless possibilities for enhancing spaces aesthetically. Its suitability for different design needs makes it a preferred choice for industries seeking both practicality and visual impact.
Pros and Cons of FRP Fiberglass Grating
Advantages
- Lightweight Nature: FRP grating weighs significantly less than steel, making it effortless to handle and install without heavy equipment. This feature reduces labor costs and simplifies the setup process.
- Corrosion Resistance: Unlike steel grating that may require regular maintenance, FRP grating is corrosion-resistant to chemicals, saltwater, and extreme weather conditions. This durability ensures long-term cost savings post-installation.
- Low Maintenance Costs: Post-installation, FRP grating demands minimal upkeep expenses compared to steel alternatives. Its robust construction eliminates the need for frequent maintenance, offering a hassle-free solution for industries.
- High Strength-to-Weight Ratio: With a high strength-to-weight ratio, FRP grating provides exceptional load-bearing capabilities while being lighter than traditional steel options. This balance of strength and weight makes it a reliable choice for various applications.
Disadvantages
- Higher Production Cost: The initial production cost of FRP grating is higher than steel due to the materials used in its manufacturing process. However, the long-term maintenance-free aspect of FRP can offset this initial investment over time.
- Limited Heat Resistance: While FRP grating excels in many areas, it has limitations in extreme heat conditions compared to steel. Industries requiring high heat resistance may need to consider alternative options for specific applications.
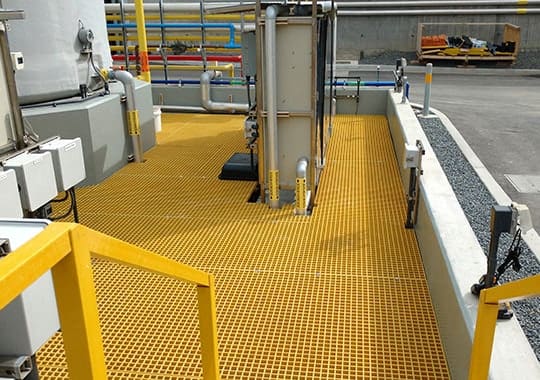
Pros and Cons of Steel Grating
Advantages
- Expertly crafted from fiberglass-reinforced plastic, OceanFRP Grating ensures long-lasting durability and safety in industrial and commercial settings.
- Lightweight yet strong, steel grating offers a reliable solution for heavy-duty applications where robust structural support is essential.
- Resistant to chemicals, fire, and UV damage, steel grating provides a durable option for environments requiring high-strength materials.
- With its high load-bearing capacity and rigidity, steel grating is ideal for applications demanding stability and longevity in various industries.
Disadvantages
- While offering exceptional strength, steel grating may pose challenges in terms of weight during installation compared to lighter alternatives like FRP grating.
- The maintenance requirements of steel grating can be higher than those of corrosion-resistant materials like FRP, potentially leading to increased upkeep costs over time.
- In environments with extreme heat conditions, the limitations of steel grating may impact its performance compared to materials designed specifically for heat resistance.
- The initial cost investment for steel grating might be higher than alternative options due to the manufacturing process and material expenses.
Environmental Impact
When considering the sustainability aspect of FRP fiberglass grating versus steel grating, it becomes evident that each material offers unique environmental benefits. GRP gratings, known for their lightweight construction and durability, contribute to reducing carbon footprints in industries where weight reduction is crucial. On the other hand, steel gratings excel in heavy-duty environments, ensuring stable footing and protection against impact.
Sustainability of FRP Fiberglass Grating
- Lightweight Construction: The use of fiberglass in FRP grating results in a lighter product compared to traditional steel options. This weight reduction not only simplifies transportation and installation processes but also minimizes the carbon footprint associated with heavy materials.
- Corrosion Resistance: The corrosion-resistant properties of FRP grating reduce the need for frequent maintenance, leading to long-term sustainability by minimizing waste and resource consumption.
- Recyclability: GRP gratings are recyclable materials that can be repurposed or reused, promoting a circular economy approach that reduces environmental impact.
Sustainability of Steel Grating
- Durability: Steel grating’s robust construction ensures longevity and structural stability in various applications, contributing to sustainable solutions that require minimal replacements over time.
- Recycling Potential: While steel is a recyclable material, its production process involves significant energy consumption. However, the recyclability of steel gratings at the end of their lifecycle supports sustainable practices within industries.
Recycling and Disposal Considerations
- When it comes to disposal considerations, both FRP fiberglass grating and steel grating offer environmentally friendly options. Proper disposal methods ensure that these materials can be recycled or repurposed efficiently.
- Recycling initiatives play a vital role in reducing waste accumulation and promoting eco-friendly practices within industrial sectors. By choosing materials like GRP gratings or steel gratings with recycling potential, industries contribute to a more sustainable future.
Applications and Industry Usage
Industries across various sectors benefit from the unique properties of FRP grating and steel grating, each excelling in specific applications. Understanding where each type shines is crucial for making informed decisions that align with operational needs and long-term cost-effectiveness.
Sectors where FRP fiberglass grating excels
- Chemical Plants: The corrosion-resistant nature of FRP grating makes it a preferred choice in chemical plants where exposure to harsh chemicals is common. Its durability and resistance to corrosive elements ensure a reliable solution for demanding environments.
- Water Treatment Facilities: In water treatment facilities, where resistance to water-related corrosionis essential, FRP grating stands out as an ideal option. Its ability to withstand moisture and corrosive substances makes it a durable and cost-effective choice.
- Industrial Walkways: The anti-slip surface of FRP grating enhances safety in industrial walkways, providing secure footing for workers in areas where traction is crucial. Its lightweight nature simplifies installation while offering robust structural support.
- Commercial Buildings: From office buildings to shopping centers, the versatility of FRP grating allows for diverse applications that require both aesthetic appeal and functionality. Its customization options cater to various design needs while ensuring long-lasting performance.
- Offshore Platforms: Due to its lightweight construction, corrosion resistance, and high strength-to-weight ratio, FRP grating is well-suited for offshore platforms in the oil & gas industry. It provides stability and safety in challenging marine environments.
Sectors where steel grating is preferred
- Bridge Construction: Steel grating’s strength, durability, and resistance to pests make it an optimal choice for bridge flooring applications requiring robust structural support under heavy loads.
- Industrial Facilities: In industrial settings where stability and longevity are paramount, steel grating offers a reliable solution for walkways, platforms, ramps, and trench covers. Its high load-bearing capacity ensures safety in high-traffic areas.
- Heavy-Duty Environments: Steel grating excels in environments with extreme conditions or heavy loads due to its rigidity and durability. Industries requiring materials that can withstand intense pressure often opt for steel solutions.
- Structural Support: For applications demanding stable footing and structural integrity, such as platforms in manufacturing facilities or warehouses, steel grating provides the necessary support for operational efficiency.
Case studies or examples
- A study comparing the use of FRP gratings versus steel gratings highlighted the long-term cost-effectiveness of FRP due to its low maintenance requirements post-installation.
- Advantages of FRP gratings were evident in various applications across industrial, commercial, and residential sectors due to their corrosion resistance, lightweight nature, versatility, and long lifespan.
- Factors driving market growth emphasized the sustainability benefits of FRP gratings like low life cycle costs, lightweight construction reducing carbon footprints, high strength-to-weight ratio benefiting industries seeking durable solutions.
- GRP gratings were recognized as a cost-effective alternative to steel with lower maintenance needs contributing to practicality and sustainability within different industry segments.
- The versatility of FRP gratings was showcased through their application diversity ranging from chemical plants needing corrosion resistance to commercial buildings requiring aesthetic appeal combined with functionality.
Conclusion
In summary, the comparison between FRP fiberglass grating and steel grating highlights the distinct advantages of each material. FRP grating, known for its lightweight nature, corrosion resistance, and high strength-to-weight ratio, offers a cost-effective and durable solution for various industries. On the other hand, steel grating excels in applications requiring robust structural support and durability against heavy loads.
Based on specific needs and applications, it is recommended to consider FRP grating for environments where corrosion resistance, low maintenance costs, and impact resistance are vital. Industries such as chemical plants, water treatment facilities, and commercial buildings can benefit from the versatility and long-term cost-effectiveness of FRP grating.
For projects demanding high load-bearing capacity and stability under extreme conditions, steel grating remains a reliable choice. Bridge construction, industrial facilities, heavy-duty environments, and areas requiring structural support can leverage the strength and durability of steel gratings effectively.
When selecting between FRP fiberglass grating and steel grating, evaluating factors like environmental conditions, maintenance requirements, safety considerations, and long-term cost implications is crucial to making an informed decision that aligns with specific project needs.
FAQs
-
What is the research methodology used to estimate and forecast the FRP grating market?
The research methodology employed for estimating and forecasting the FRP grating market follows a bottom-up approach. This approach involves analyzing individual segments and subsegments to arrive at the estimated values comprehensively.
-
How does regulatory analysis play a role in providing cross-segmentation in applicable scenarios or markets?
Regulatory analysis serves as a crucial aspect in ensuring compliance and understanding market dynamics. While it may not directly provide segmentation, it influences decision-making processes within specific markets, guiding strategic directions effectively.
References
For further exploration and detailed insights into the comparison between FRP Fiberglass Grating and Steel Grating, readers are encouraged to delve into additional resources. These sources provide in-depth analyses, case studies, and industry perspectives that complement the information presented in this blog section.
In conclusion, the comparison between FRP fiberglass grating and steel grating reveals distinct advantages for various industries. FRP materials have proven to provide a dramatically greater lifespan than traditional materials, excelling in unforgiving environments. Choosing the right material is crucial for stability, durability, cost-efficiency, and environmental impact. For industries seeking corrosion resistance, low maintenance costs, and impact resistance, FRP grating is a wise investment. On the other hand, steel grating remains a reliable choice for projects demanding high load-bearing capacity and stability under extreme conditions.